manufacturers of concrete façade elements
In addition to the building companies that took part in the model home expositions (e.g. Delmulle, Elbeko, Declerck en Zonen, Rhodius-Deville, R. Maes, Roosen, Caroni-Lecomte, Van Den Bogerd-Elst, Van De Kerckhove’s Prefa, Usidour, and Koramic), many other Belgian companies produced façade panels in architectural concrete (not necessarily with a complete house behind it) during the 1960s and 1970s. In 1975, the catalogue of the UACB listed 31 manufacturers of façade frames, parapets, and flat panels in architectural concrete. Some of the more significant market players were Antwerpse Machinesteenbakkerijen, CBR-Ergon, Eurobeton, Marbra-Lys, Seghers Prefalith Beton, and Kunststeenfabriek Vandewalle. Most of these manufacturers specialized in diversity, meaning that they all tried to offer the broadest possible range of products, instead of focusing on one particular style or element. The 1975 catalogue shows that most companies produced different types of panels, both loadbearing and non-loadbearing, which came as single wall elements or sandwich elements, with or without insulation in between layers. The four main surface options were smooth, washed, acid-scoured, and sandblasted concrete. Manufacturers also offered façade elements with various connections and details, and made of concrete with varying chemical compositions. Fillers and additives like plasticizers, bond accelerators or retarders, air entraining agents, coloured pigments, glass fibres, etc. allowed manufacturers to manipulate the strength; thermal and acoustical isolation; weight; colour; texture; and even the transparency of the material. By (small) variations in the materials, forms, proportions, and techniques, innumerable types of concrete panels were produced. A seemingly infinite number of choices was something that the industry explicitly featured in its advertising.
The company Antwerpse Machinesteenbakkerijen holds a special position in this list because it specialized in brick manufacture rather than concrete. Nevertheless, the company produced a composite panel Pandal combining bricks and concrete. The panel consisted of a pre-stressed concrete outer layer and an inner core of masonry blocks. It resisted compression forces up to 34.32 N/mm², and the hollow core gave it good insulating properties compared to regular concrete panels (1.63 W/m²K). The exterior surfaces could be white concrete with a smooth surface or textured with exposed flint. The panels were typically 4, 5, or 6 m wide (maximally 10 m) by 60 cm high and 12 cm thick, and weighed 165 kg/m². An unusual feature of this panel was that it could be demounted and reused: they were usually installed by stacking one on top of the other (with a tongue and groove fitting) and attaching them to a steel, concrete, or timber skeleton with reversible, galvanized steel hooks. Another installation option was to slide them into profiled columns and fill the joints with mortar; in this case, they could not be demounted.
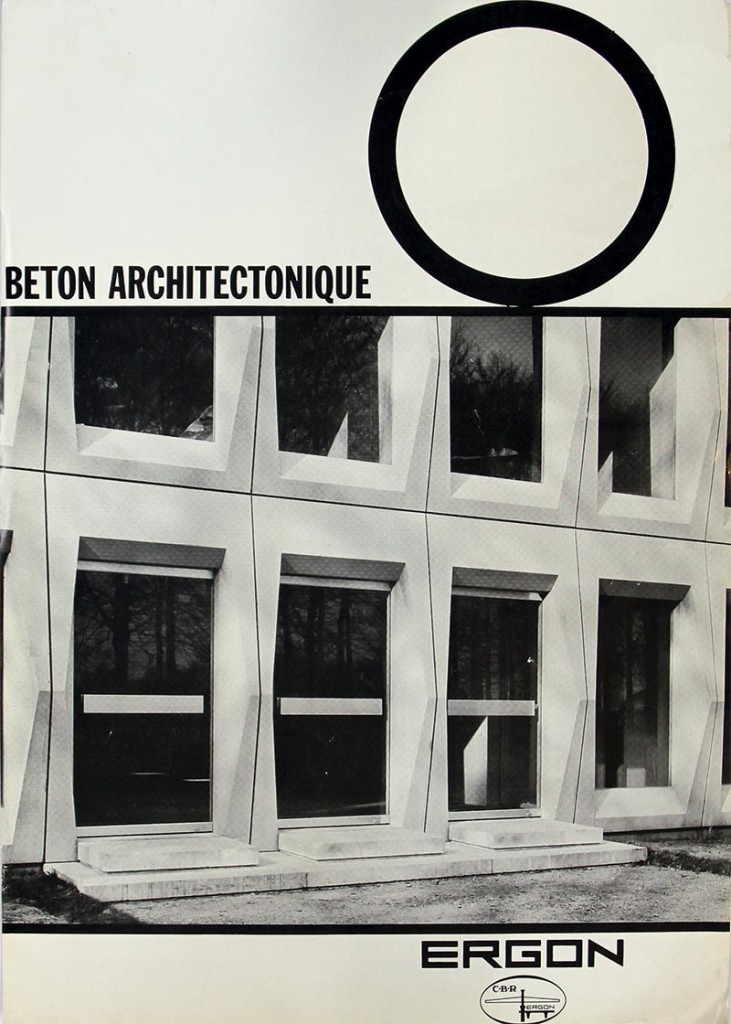
CBR-Ergon, a daughter company of the cement manufacturer CBR, was established in 1963 to produce precast concrete elements. CBR-Ergon mainly focused on standardized structural products such as beams, columns, and hollow core slabs, yet almost immediately after its establishment, the company also set up a research and production line for façade elements in decorative and architectural concrete. Research connected with these elements focused on the composition of the mixture, compaction of the wet concrete, formwork, texture and finish of the elements. With some remarkable offices in architectural concrete designed in collaboration with architect Constantin Brodzki, Ergon became one of the major players in this field. The most striking realisations by CBR-Ergon were in office buildings rather than residential buildings.
Established in 1964 in Massenhoven, Eurobeton became an important manufacturer of architectural precast concrete. The firm’s range mainly consisted of façade frames, parapets, and flat panels for offices, public buildings, etc. Eurobeton used both timber and metal formworks fixed to vibration tables, and portable formworks in plastic and metal, for fabricating their products.
Marbra-Lys, established in Kortrijk in 1913, was originally a supplier of building materials. During the 1950s, the company moved to Harelbeke, and their emphasis shifted to the industrial production of tiles, claustra, and stairs in marble mosaic, artificial stone, and artificial marble Marbralyth. From the 1960s onwards, the company added façade elements in architectural concrete to its product line, especially for applications in office and apartment buildings. Architectural concrete was precast in a 150 m-long production hall, which included equipment for vibrating and steaming the concrete. At the end of the 1990s, the company Decomo in Moeskroen took over Marbra-Lys’ department for architectural concrete.
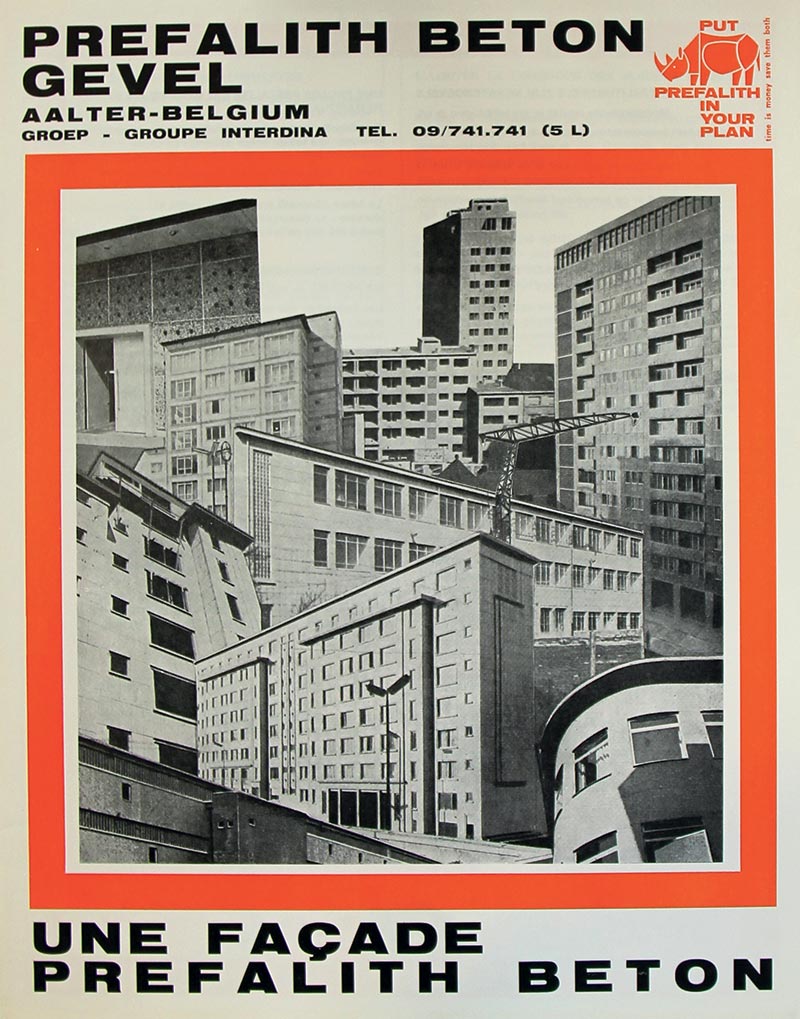
Seghers Prefalith Beton in Aalter started with the production of architectural concrete in 1956. The acquisition of new production sites in 1967-1968 in Aalter coincided with a considerable expansion, including extensive new facilities to produce architectural concrete and fibre reinforced concrete, using the latest scientific and industrial equipment. It became one of the major producers of architectural concrete in Belgium, and also exported to the Netherlands and France. The production process for architectural concrete was organized according to a 24 hour cycle. The formwork was filled at a fully automated mixing plant. After the elements were compacted on heavy vibration tables, they were transported into a climate tunnel for curing. At the end of the tunnel, the elements were demoulded and underwent a surface treatment. The company published their own building specifications, with specific recommendations for architectural precast concrete. These included specifications related to insulation, joints, connections, anchors, surface treatment, and execution of a prototype. A typical façade panel in architectural precast concrete consisted of two layers: first a decorative layer, at least 10 mm (with rolled or crushed quartz or porphyry), was cast, followed by a layer of regular concrete. The panels were 7 cm thick and up to 2.50 m long; for larger panels, stiffening ribs or ridges were provided. Seghers Prefalith Beton also manufactured sandwich panels consisting of a 5 cm panel of decorative concrete, 2 or 3 cm of polystyrene, and 5 cm of lightweight concrete. These (insulating) panels were used to construct office, residential, and public buildings such as schools and municipal administrative centres. In 1985, the company was taken over by Loveld in Aalter.
The artificial stone company Kunststeenfabriek Vandewalle was established in 1960 in Roeselare by the same family that had already founded a tile factory in 1920. Vandewalle’s products developed from relatively small, decorative elements in artificial stone, to load-bearing, high-quality, and fully finished elements reaching from floor to floor. One of their products was Quartzolite, a particular type of concrete based on natural quartz stone that was watertight and frost-proof. Quartzolite was used to make façade claddings (usually 4 cm thick), thresholds, door frames, capstones, among other things.